Designing Custom Machine Control Systems for Maximum Efficiency
Written by Automation Services Inc. | read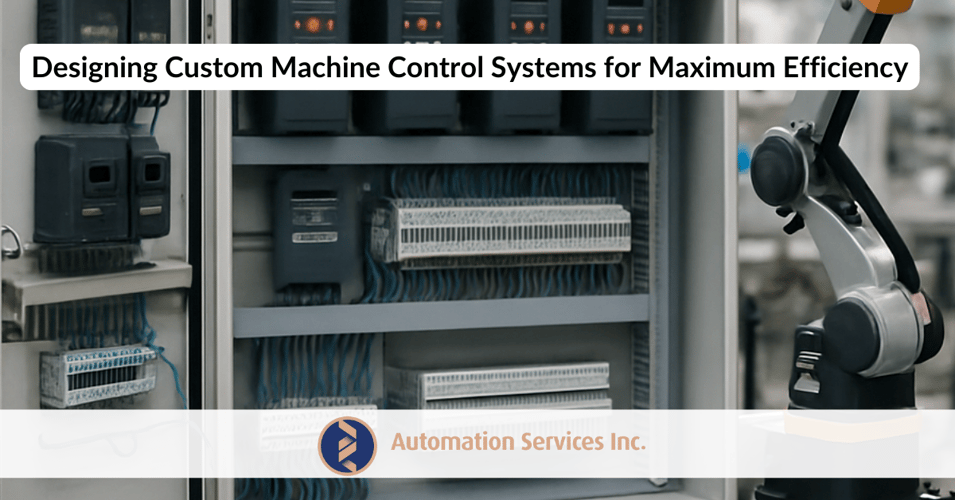
Custom control systems are essential for enhancing machine performance and efficiency in industrial automation. Designed to meet precise requirements, these systems deliver exceptional reliability, scalability, and long-term productivity. For OEMs, machine builders, and automation engineers alike, mastering the design and implementation of custom control systems is key to unlocking optimal results.
What Are Custom Machine Control Systems?
Custom control systems are tailored solutions designed to manage, monitor, and optimize industrial machinery with precision. Unlike generic, off-the-shelf options, these systems are specifically engineered to meet the unique needs of a machine or production line, seamlessly aligning with operational requirements. Featuring advanced controllers, user-friendly software interfaces, and high-precision sensors, custom systems take automation performance to the next level.
Custom control systems often include advanced programmable logic controllers (PLCs) or distributed control systems (DCS) for real-time monitoring and precise control, user-friendly software interfaces for intuitive operation, and high-precision sensors to gather critical data. These systems can be configured to handle complex automation tasks, such as synchronizing multiple machines, managing variable production rates, or automating intricate quality checks.
By addressing common challenges like production bottlenecks, inefficiencies, machine downtime, and inconsistent quality, custom control systems enable businesses to streamline their operations, reduce operational costs, and enhance productivity. Furthermore, they can be designed with remote monitoring capabilities, allowing operators to access data and control systems from anywhere, improving decision-making and response times.
Whether it's for manufacturing, energy, food processing, or any other industry, these bespoke solutions take automation performance to the next level, ultimately driving growth and competitive advantage in a rapidly evolving industrial landscape.
Key Design Considerations
Developing custom control systems demands close consideration of several essential factors:
Feature |
Description |
Details/Examples |
Scalability |
The system must adapt to future changes, such as increased production demands or the addition of new machinery. |
- Should handle higher production volumes seamlessly.<br>- Easily upgradeable to incorporate advanced machinery. |
Compatibility |
Seamless integration with existing equipment and software ensures smooth operation without costly disruptions. |
- Must support legacy systems and modern software.<br>- Minimize downtime during integration. |
User Requirements |
Designs should reflect user goals, such as achieving faster processing times, reducing human error, or optimizing energy use. |
- User-friendly interface for operators.<br>- Energy-efficient solutions to lower operating costs.<br>- Automation to reduce manual tasks. |
Ecosystem Fit |
Ensures the system integrates into the broader industrial environment effectively while meeting specific operational needs. |
- Aligns with industry standards.<br>- Supports future technological advancements in industrial automation. |
Impact on Machine Performance and Uptime
- Improved Automation Performance: Custom control systems do more than just handle basic task automation; they are designed to enhance overall system efficiency and reliability by adapting to specific operational needs. These systems can be fine-tuned to integrate seamlessly into existing workflows, ensuring smoother operations and greater productivity.
- Reduced Machine Downtime:
- Real-time monitoring allows operators to identify and address potential issues before they result in costly failures. By continuously analyzing system performance, these tools can detect early warning signs and recommend timely interventions.
- Proactive maintenance strategies help reduce unplanned downtime and extend the lifespan of critical machinery, preventing disruptions and maintaining consistent production output.
- Enhanced Industrial Control Efficiency:
- By fine-tuning machine parameters, custom control systems ensure that equipment operates at its peak performance, optimizing output while reducing waste and inefficiencies.
- These systems can significantly increase production rates while maintaining strict adherence to high-quality standards, enabling industries to meet growing demands without compromising on product integrity.
Integrating with Existing Infrastructure
One of the challenges in deploying custom control systems lies in ensuring compatibility with existing infrastructure. Integration requires careful planning and execution to avoid disruptions in operations. Strategies for achieving smooth machine control integration include:
- Conducting a thorough audit of the current infrastructure to identify potential bottlenecks or limitations.
- Designing modular control systems that can be introduced piece-by-piece without halting production.
- Training teams to familiarize them with new functionalities and interfaces.
By addressing these challenges, businesses can harness the full potential of their custom control systems without sacrificing productivity during the transition.
Efficiency Gains and ROI
Investing in custom control systems delivers tangible returns. The enhancements in industrial control efficiency translate directly into cost savings, while improvements in automation performance reduce time and material waste.
Key efficiency gains include:
- Significant energy savings through optimized machine performance, reducing operational costs, and supporting sustainability initiatives.
- Lower maintenance expenses enabled by advanced predictive monitoring, which identifies potential issues before they occur, minimizing downtime and repair costs.
- Enhanced overall equipment effectiveness (OEE), driving greater productivity and efficiency by maximizing machine uptime, improving output quality, and streamlining processes.
Elevate Your Efficiency with ASI
Custom machine control systems aren’t just tools; they’re the key to optimizing your processes and maximizing efficiency. At Automation Services Inc., we don’t just deliver solutions—we engineer systems that empower your business to surpass its goals. With nearly three decades of experience and long-term partnerships spanning over 20 years, we provide end-to-end services, from design and engineering to control panel build, testing, and installation.
Whether you need advanced robotics, municipal water control systems, or automated machine controls tailored to your unique requirements, our expertise spans across industries like food, medical manufacturing, heavy industry, marine, and more. Our proven track record of precision and reliability makes us a trusted partner for businesses seeking high-performance systems.
Don’t settle for standard when you can have custom-crafted excellence. Partner with Automation Services Inc. today to bring your next project to life. Contact us now to begin building your cutting-edge system!